Over 30% of global carbon emissions are produced by construction. To meet national and international climate targets, the UK therefore needs to radically rethink the materials with which it builds. How to Build a Low-Carbon Home – a new display at the Design Museum, London – explores the ways in which ancient building materials could contribute to this transformation. Replacing concrete and steel with stone, for example, could be key to building a low-carbon future. Our coordinator Leilah Hirson-Comley spoke with Steve Webb, founder and director of Webb Yates Engineers and key contributor to the How to Build a Low-Carbon Home display, to learn more.
LHC
To begin, can you introduce yourself?
SW
I am a civil and structural engineer, but I’ve also worked as a tunnelling and site setting out engineer on London’s Jubilee line and as a designer for Whitby Bird and Santiago Calatrava. 18 years ago, Andy Yates and I started up Webb Yate Engineers, having always been interested in embodied carbon and reducing the carbon footprint of the structures we design. Last year, you might’ve seen the stone beam we displayed at the Royal Academy’s summer exhibition. That beam had around 1/15th of the carbon of the steel equivalent – so, very much less carbon – and won us the CDUK Award for Architecture.
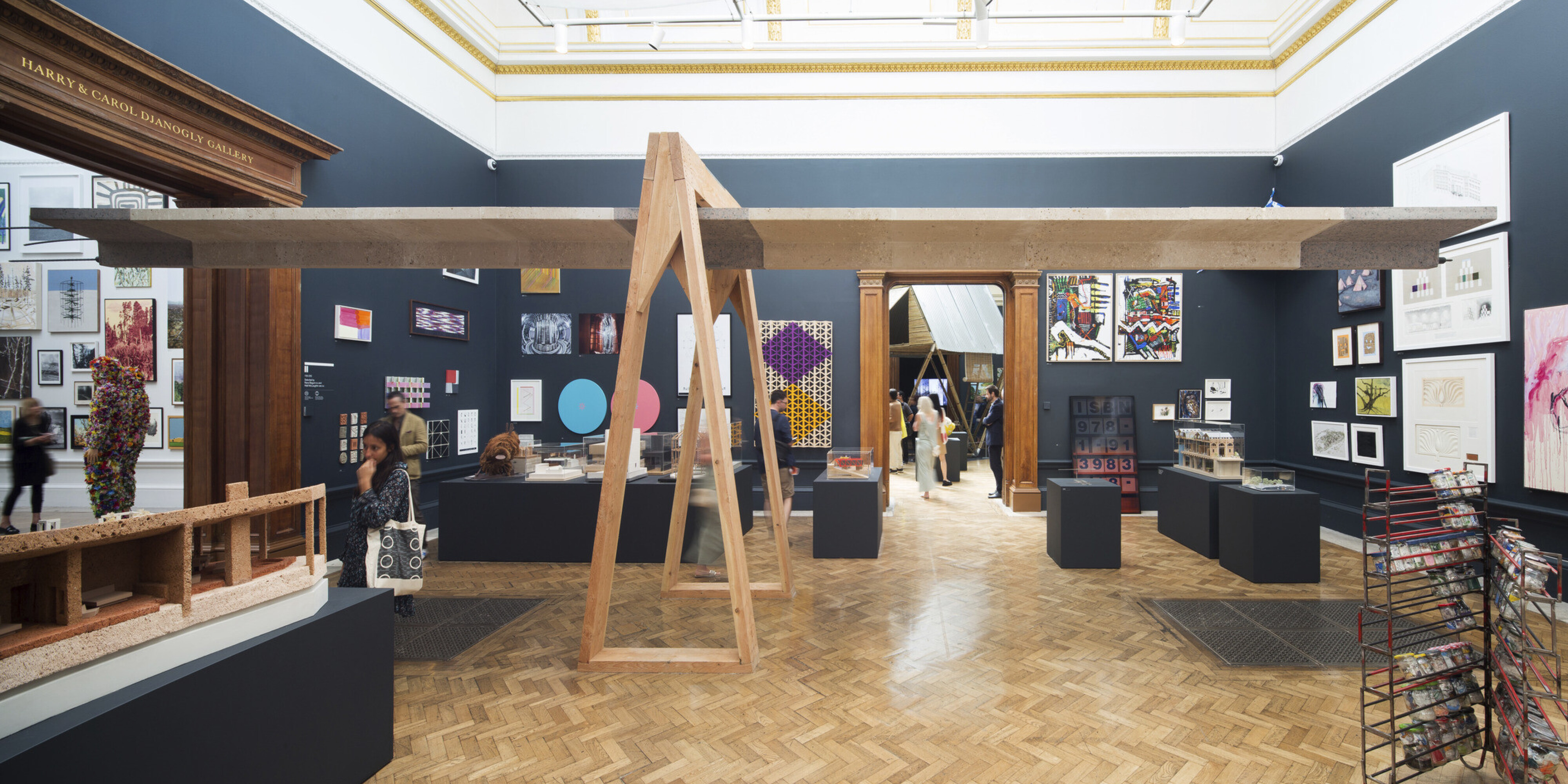
LHC
A lot of your work is focussed on reducing the environmental impact of construction. Why does the industry have such a high carbon footprint?
SW
Construction is responsible for an enormous amount of global warming. As a sector, we are deeply steeped in the fossil-fuel era; everything we make is produced using coal and gas. Ceramic, brick, steel, concrete, aluminium, glass – these are all fossil-fuel era materials, and they have been the predominant building materials of the last 200 years. But in the previous eight millennia of construction, we didn’t have any of those materials. Instead, construction centred around the use of timber and stone – more natural materials which have a far lower carbon footprint. This is because the energetic processes to transform these materials into other things simply didn’t exist.
Webb Yates have been working with stone mason Pierre Bidaud for a long time. We started off designing wooden versions of traditional stone cantilever stairs, and then Pierre gave us a job designing real stone stairs. He was really keen to sell free-standing structures because not everyone has a wall next to their flight of stairs. So, we started experimenting with post-tensioning; putting steel cables through the treads to make them stand up as structural stone stairs. One day, I began worrying that the stone might be bad for the environment because it’s such a heavy and exclusive material, but when I looked into it, I discovered that it actually has a really low carbon footprint – one third of the carbon footprint of concrete, though it is generally two or three times stronger.
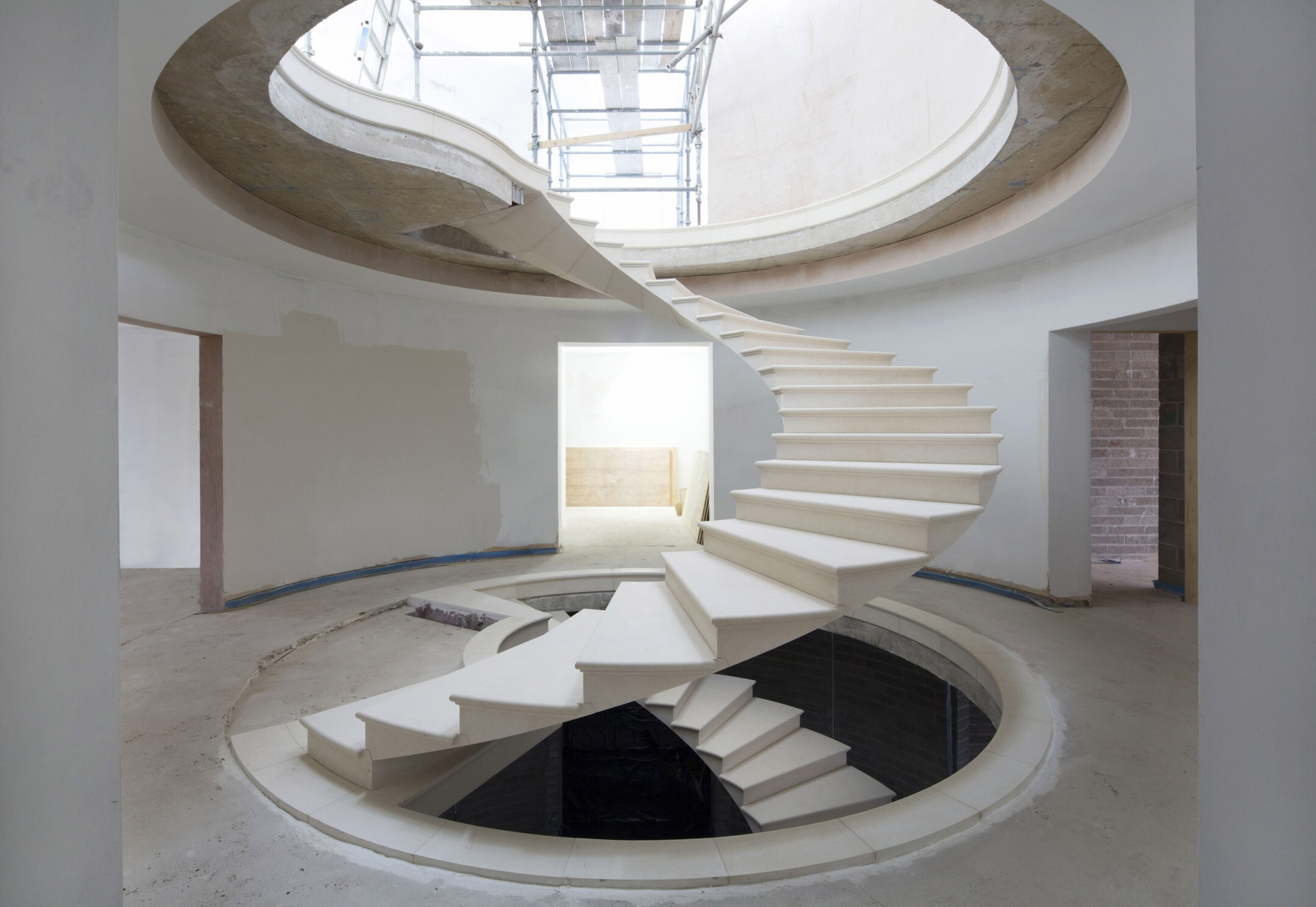
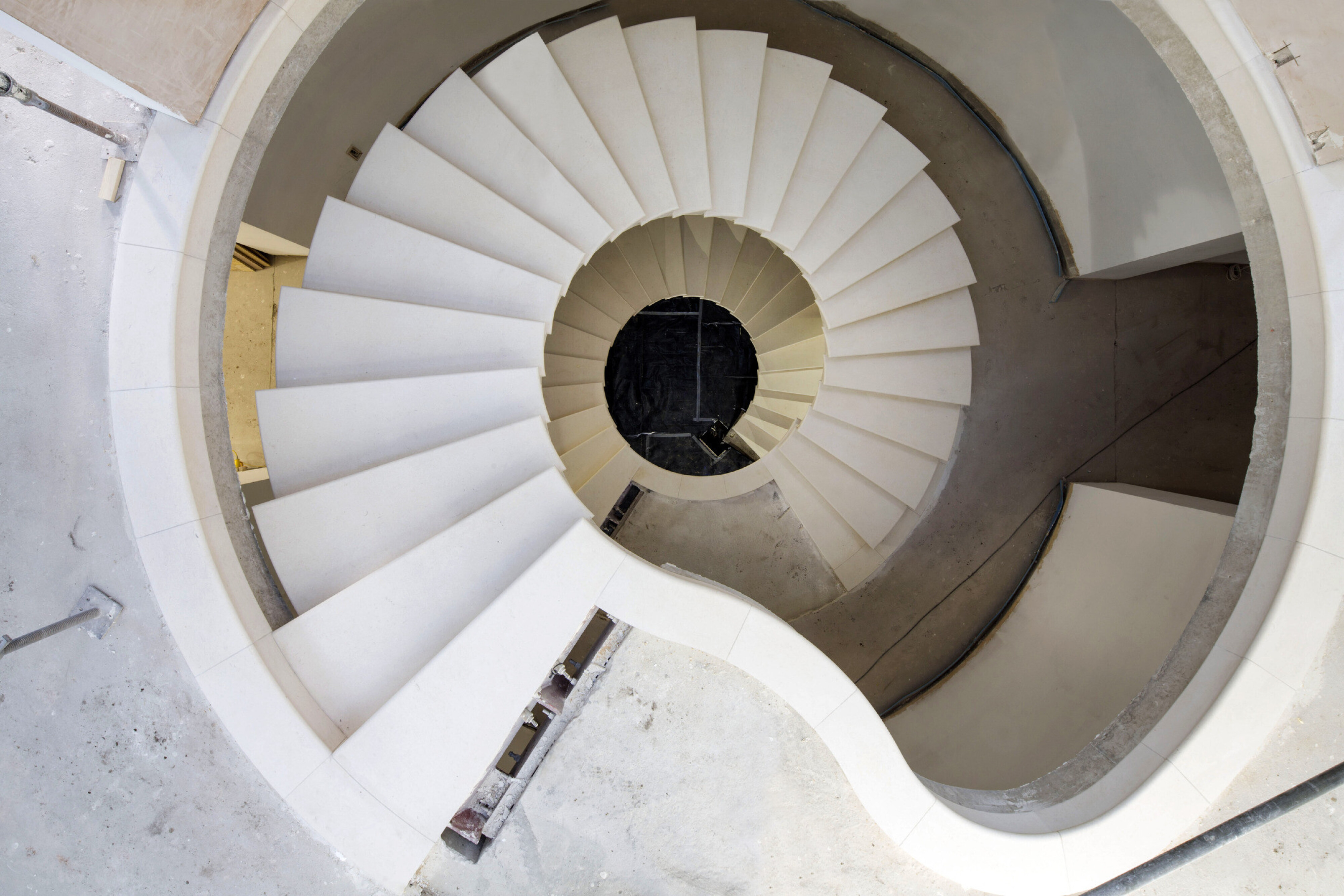
SW
To make concrete, we take a block of limestone with the strength of 120 newtons, we crush it, we burn it with gas, we mix it with fresh water and sharp sand – both of which are in short supply – we put up formwork and reinforcement, we use releasing agents and vibration, and 28 days later we have a piece of concrete with the strength of 40 newtons. So, we take a very strong material, and we throw all these energetic processes at it, and we end up with a much weaker material. Materially, concrete is inferior to stone in many respects: durability, fire, behaviour, strength, stiffness. It is an inferior facsimile of stone; stone is much better.
Working with Pierre and The Stonemasonry Company, we’ve had the opportunity to develop techniques for analysing, designing and building with stone. The helical staircases were really challenging, but we discovered that a bog-standard stone beam is actually quite simple. You take stone blocks, put them end to end, drill a hole through the middle, pull a cable through that hole, pull the cable tight and then build. So, it’s completely technically feasible to swap concrete or steel beams with stone beams; concrete slabs with stone slabs; concrete walls with stone walls. We’re even looking at cutting waste stone into brick-shaped blocks to replace ceramic bricks, and they look exactly the same as clay masonry. There’s an inherent stupidity in cutting up a big piece of stone to make a tiny piece of stone, and then spending time sticking it back together again, but the underlying idea is that we can replace high-energy materials with low-energy alternatives.
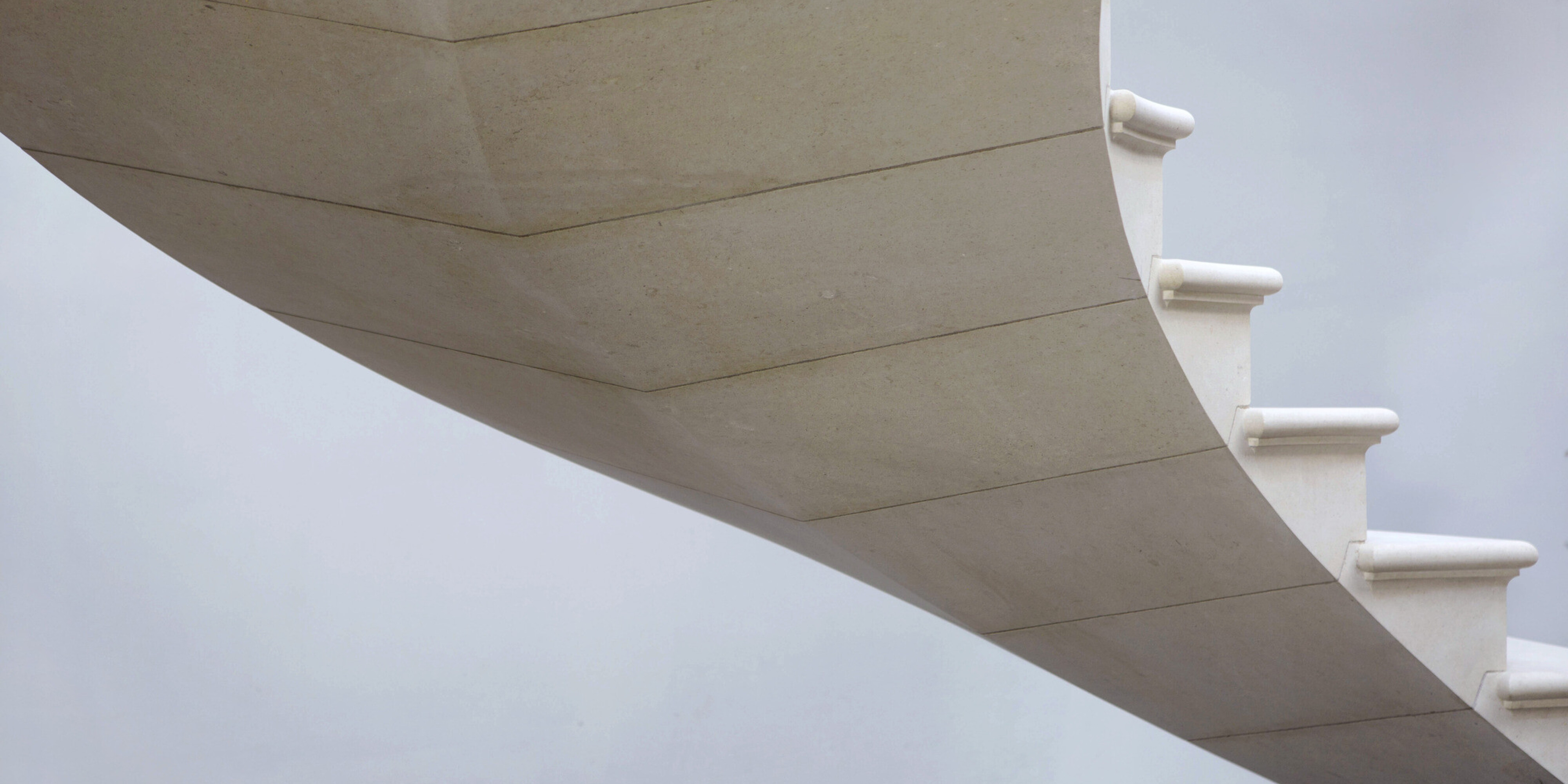
LHC
We need quarries in order to source stone – by creating lots of new quarries, is there a risk we will end up damaging our landscapes?
SW
Every construction material we use now, possibly with the exception of timber – though trees also come out of the ground – already comes out of the ground. The material used to make concrete is stone so we’re digging up stone anyway; we’re just smashing it up and reconfiguring it whereas we could cut it out of the ground more carefully and use it as it is.
When we think about environmental impact on the land, Edinburgh is a great example to use. Craigleith Quarry, from which Scotland’s big stone city is made, is currently underneath a Sainsbury’s carpark. So not only is it tiny compared to the area of the city – it’s gone, invisible. Surrounding Edinburgh, though, you can see lots of big green patches of monocultural forestry which are quite environmentally impactful. After 25 years, a tree produces 1.5 cubic metres of seven newton timber, but underneath that tree might be 500 cubic metres of 100 newton stone that you can remove in just three months.
You can also return a quarry to nature by filling the hole up again with mud (or rubbish or demolition) or leaving it open to become a lake. Nature is full of quarries: valleys, cliffs and rocks – there’s nothing unusual about exposed rock in nature. It’s not a malignant thing. Obviously, if you fill the quarries with sulphuric acid or contaminate them, that’s a problem. But normally, quarrying is quite clean – it’s just rock, dust and water. There’s a huge perceptive allergy to quarrying for stone but if you consider it in the round, I don’t think it’s a problem.
LHC
How can stone construction be sustainably scaled up in the future, and how can an engineering practice support this?
SW
The investment required to make a stone beam factory is peanuts. In fact, you can fit the tools you need to make a stone beam – a disc cutter, a drill, a cable and a hydraulic jack – in a suitcase. If you want to make a steel beam, however, you have to go to Brazil or Australia, dig a hole, go to a blast furnace and a blending mill and a rolling mill and a fabrication shop, and then weld it all together. So, procuring a steel beam depends on a much larger capital investment. There are also far fewer processes involved in making stone post-tension beams than steel beams or concrete beams, so somebody with expertise would be able to automate stone beam production to make it very, very quick. There’s absolutely no reason why that process can’t be cheaply industrialised.
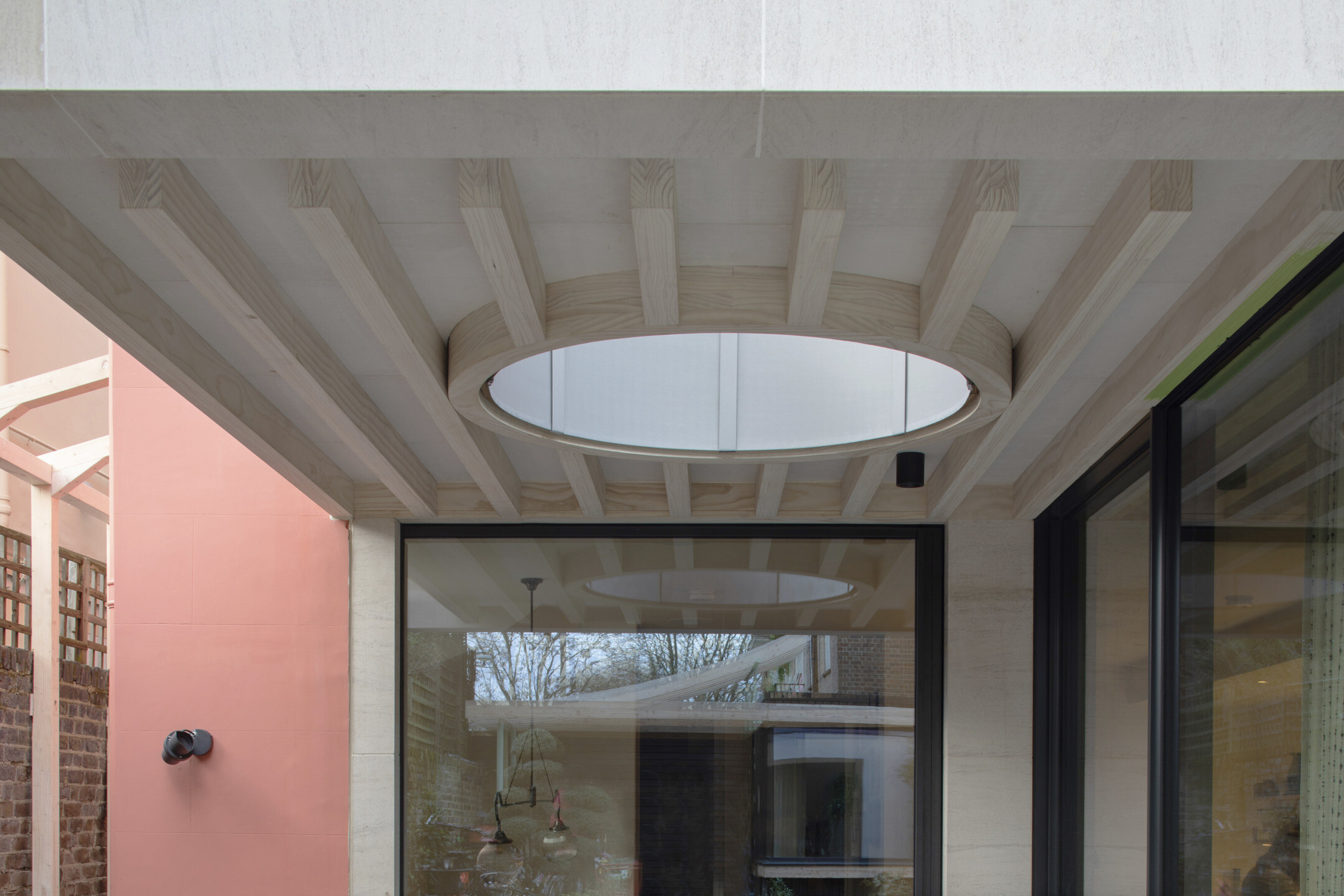
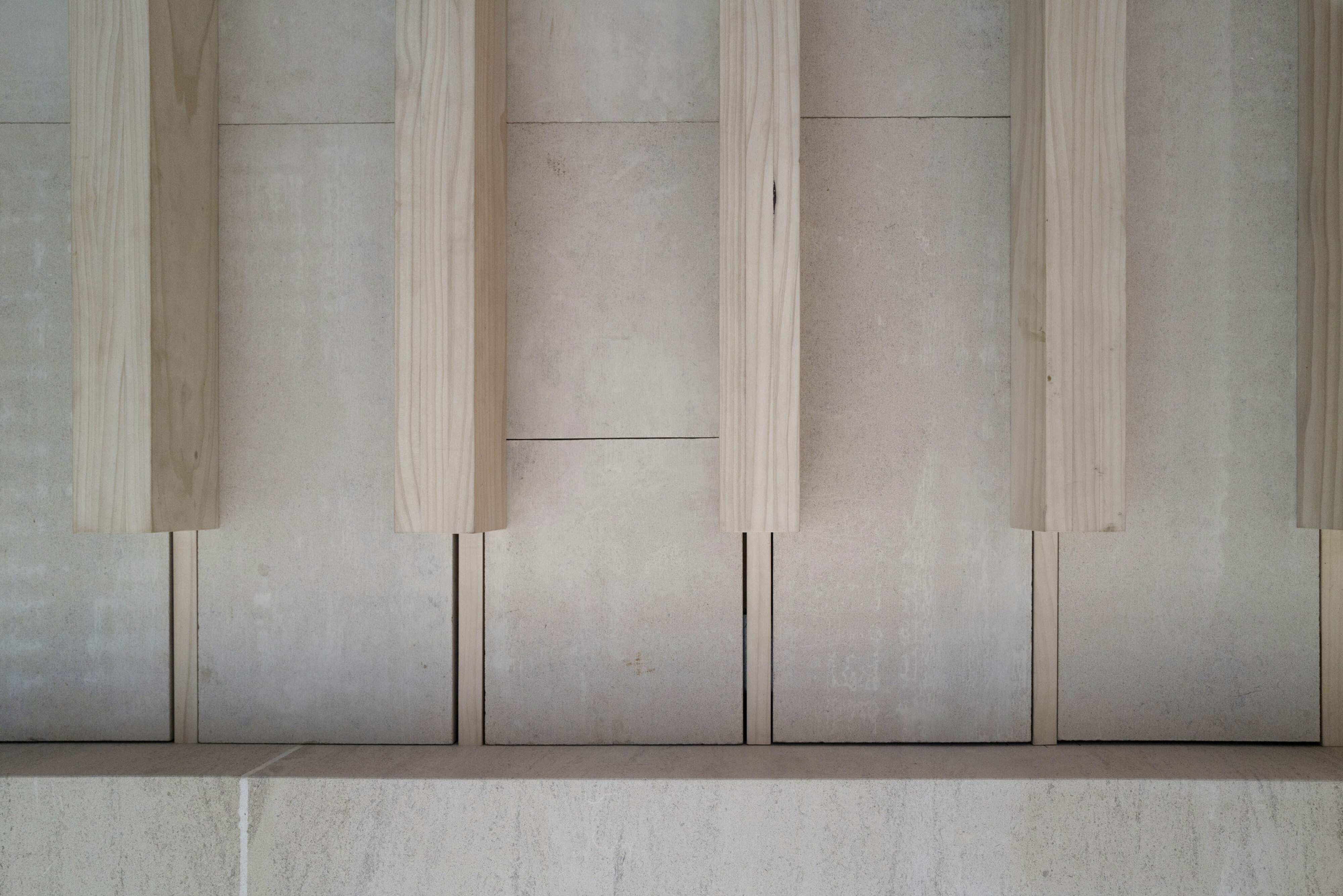
SW
As a commercial practice, Webb Yates will push timber and stone as alternatives to steel and concrete on most projects. There will only be a partial uptake but we would love to design more of those buildings and we’re advocating for and writing and talking about it. We’re also making buildings with Amin Taha and Pierre which we’re pushing to publicise further. What would be amazing would be if other engineers began to design in stone too. Half of me is like, “Oi, get off my patch!” But the other half of me feels that our knowledge should be open access and we should be teaching people how to use it because that will create a bigger market. If we’re able to transform vernacular construction from steel and concrete to stone over the next 30 years or so, that would be a monumental shift for the world and result in massive decarbonisation.
They say that engineers save more lives that doctors. Joseph Bazalgette – the man who built the sewers in London – saved millions of lives. Architects often focus on the aesthetic qualities of their buildings but many of these are actually just propagating the same materials that we’ve been using for the last 200 years. The transformative ideas will come from technological and manufacturing people, working in collaboration with architecture. If we engage technologists, builders and engineers, then we’ll be able to solve real problems. And this could make the world quite different.
LHC
Webb Yates has been a key contributor to the Design Museum’s How to Build a Low-Carbon Home display. What can visitors expect to see?
SW
We submitted a model – slightly scrappy, as it was made by me – using leftover trevertine bathroom tiles, scraps of ply-wood and an unwanted mirror. It is a mini tour de force of some of the technologies that Webb Yates have been designing and building with, and we think it is an excellent proposition for a mid-European country that has a mixture of timber and stone available. The model shows how these materials can be used together, creating a structure with a significantly smaller carbon footprint than those made from materials like concrete, brick and steel.
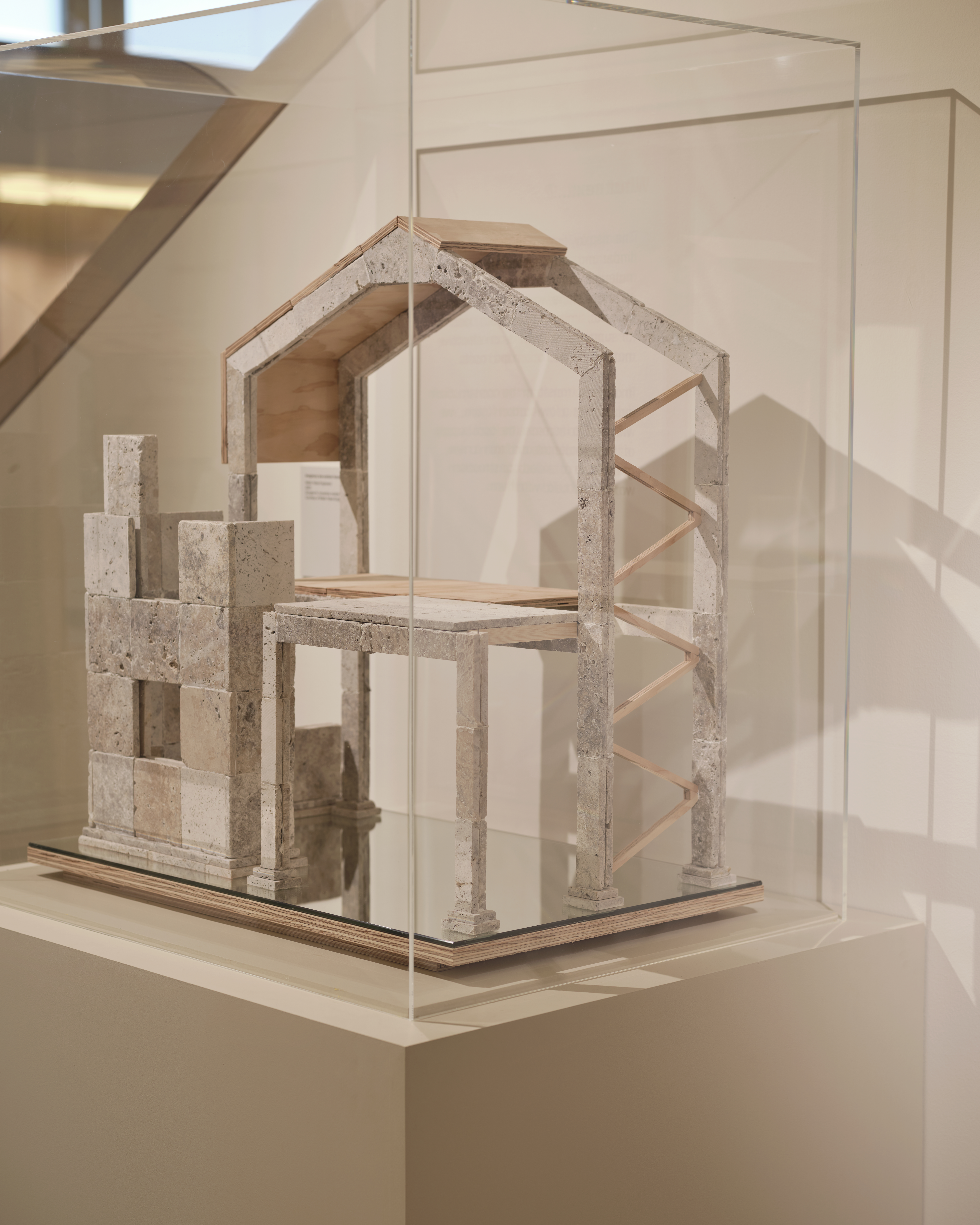
The How to Build a Low-Carbon Home display is being shown at the Design Museum until 17 March 2024.
*The interview has been edited for length and clarity.